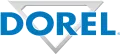
Case study by Dorel Juvenile on the use of Bonita as part of its product marketing process.
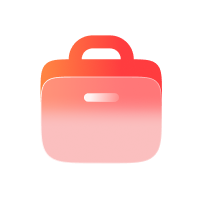
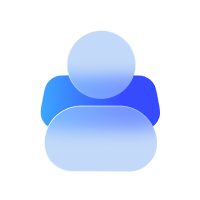
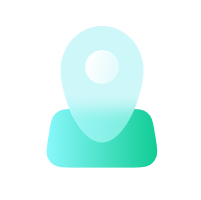
Company
Use cases
Product to market process optimisation with Bonita.
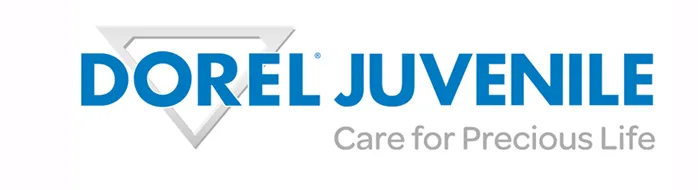
Dorel
Established in 1962 in Canada, Dorel now has 11,500 employees accross the world but remains a family group with strong values of responsible development. With a global turnover of 2.4 billion euros, the company has three distinct divisions each of which is specialized in the creation of specific items in three areas : sports and leisure, furnishings and childcare products.
Dorel Juvenile.
Dorel childcare division, Dorel Juvenile is one of the global leaders with a revenue of more than 1 billion euros and markets strong brands on the American and European markets such as Maxi-Cosi, Bébé Confort, Quinny or Safety 1st.
The company success is linked to its capacity to get customers confidence with high quality products aimed at children safety and confort.
Dorel challenges.
A very long and complex process from the decision to market a product until it is put on the shelf.
- When a new product is finalized in R&D and the decision is made to take it to market, a long chain of decisions and validations involving many units takes place: R&D, production, finance, marketing, Q&A and logistics. In all, up to thirty people may be involved in sequence for several months in this
process, which can be affected by bottlenecks and hence delays. - These processes were managed through unstructured Excel file exchanges, emails or messages from multiple communication channels, contributing to a high risk of data entry errors, missing
information and transmission slowdowns. - "Our organization workflows need to be well managed because with so many stakeholders to fuel our information systems, the risk of data entry errors, of missing information and transmission slowdowns is quite high."
Benefits of the project.
Simplification of the process, dashboard to better monitor, and better productivity.
- With the acquisition of other companies, and standardization of the information systems with a new global ERP, adding a BPM platform to manage workflows was well timed.
- Despite the complexity of the process, given the large number of relevant departments, the Bonita platform has been successfully deployed across the enterprise at the European level.
- With dashboards, decision making is easier, and they provide a better view of bottlenecks and the time needed for each part of the process.
- With the success of this process, the company is now developing new business processes. A purchasing process application has been put in place quickly, which allows employees to make erequests for computer and office supplies. This much more efficient automated workflow will eventually roll out to up to 300 people and will be joined shortly by a business travel request
process.
Dorel uses Bonita to streamline and optimize the end-to-end creation of new products.
« The organization of our process for creating products was complex, involving many business units. Bonitasoft accompanied us to effectively address this major challenge for the company.»
Olivier Clos - CIO Europe
"The Bonita platform is very reliable and easy to use. It has enabled us to greatly increase efficiency and productivity""
Olivier Clos - CIO Europe
Ready to simplify your processes with Bonita?
Every business deserves a solution that accelerates its success. With Bonitasoft, simplify, automate and transform your business processes. Take the first step towards optimal performance today. Let's talk about it?